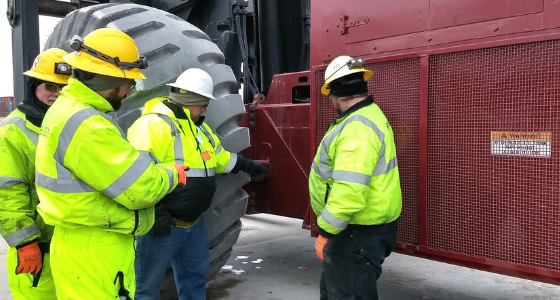
Hugg & Hall Trainer Helps Write New Industry Standards
Bob Hendricks, a trainer at Hugg & Hall Equipment Company (Hugg & Hall), recently assisted...
Bob Hendricks, a trainer at Hugg & Hall Equipment Company (Hugg & Hall), recently assisted...
Buying used equipment can be daunting. We're here to help with our handy guide! Step...
Violation: Over-Exposure to Respirable Crystalline Silica Solution There are three paths to complying to the...
Meet Susie Teague our most recent Employee Spotlight! Susie Teague works as the lead service...
Preventative Maintenance Preventative maintenance refers to precautionary work performed on equipment with the express purpose...