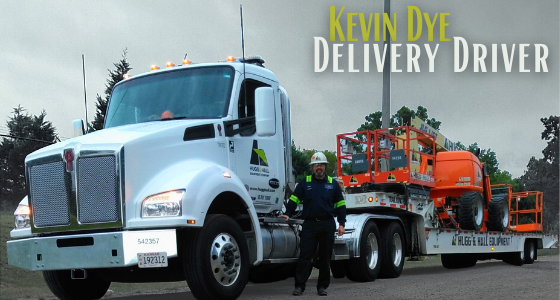
Employee Spotlight: Kevin Dye
THE ONLY WAY TO DO GREAT WORK, IS TO LOVE WHAT YOU DO! Hugg &...
THE ONLY WAY TO DO GREAT WORK, IS TO LOVE WHAT YOU DO! Hugg &...
Defining your welding process should be the first step taken when deciding on a welder....
SAY HELLO TO BRYAN HOOKS! Bryan works as an Outside Rental Salesperson in our Oklahoma...
“Ask Britney!” Meet Britney Bradshaw, Service Manager at our El Dorado branch! Britney's original spotlight...