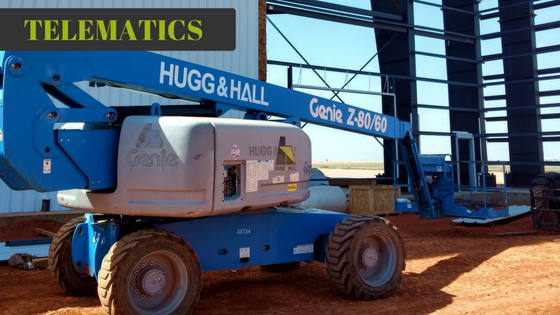
How Telematic Technology is Transforming the Equipment Industry
The use of telematic technology, i.e. telematics, is transforming the way equipment companies manage and maintain their fleets. Telematics have streamlined workplace methodologies from equipment maintenance, reporting, safety/training procedures to operations and more. Telematics combines telecommunications with data processing, storage and retrieval systems. Equipment companies are exploring the capabilities of telematics and how the technology can support more efficient business practices.
How it works
Telematics can be used to track and assess vehicles and is spearheading innovation in the equipment industry. Recently, Matt Conner, Product Support Sales Representative at Hugg & Hall Equipment Company (Hugg & Hall), spoke on how the use of telematics is reshaping the industry.
“Telematics is a technological way to assist companies in managing their industrial equipment and/or fleet,” said Conner. “It allows accurate, up-to-date business metrics at a click of mouse.”
Telematic systems can be customized to fit the varied needs of users. One example of this is in construction versus industrial equipment needs. Construction equipment tends to require satellite-based systems because, locationally, internet-based systems would be more challenging and less reliable. Industrial equipment, often used in plants and warehouses, are often connected to Wi-Fi-based systems. Conner extrapolated on how the different methods are applied.
“The difference is, construction equipment is typically found at many different job sites, so it’s not always contained under one roof,” said Conner. “That’s why satellite is utilized for construction equipment because, using this system, equipment can be pinged anywhere in the U.S. Whereas, industrial equipment, such as forklifts, are typically found under one roof and usually can use Wi-Fi and the cloud to receive information and deliver it back to the portal.”
“It (telematics) allows people, and managers, to work more efficiently,” said Conner. “It keeps them off the floors and doesn’t require them to spend as much time with operators and equipment. They can basically generate reports off of production, utilization and other key components to better manage their fleet, and possibly, their operators.”
Before the implementation of telematics, equipment assessment required more physical time at job sites and with equipment. Telematics has significantly reduced travel and assessment requirements which, in turn, has increased efficacy and productivity rates.
“Prior to telematics, if there was an issue with a piece of equipment, we had to go on site or rely on the customer to give us enough information to be able to assess issues with equipment and/or asset damage,” said Conner. “So this will free up a lot of our time and prevent us from traveling to unnecessary locations. A lot of customers, when we’re talking about contractors and construction equipment, may have twenty pieces and they might not know where that equipment is located so they might send you to Fayetteville and, in reality, it’s in Bella Vista or something like that. So we can use telematics to track locations and eliminate those issues.”
Safety features
Some capabilities of the technology include tracking operator training schedules, reminder features and safety goals; which can all be assembled in reports and exported for retention and metric tracing.
“So, there are several ways that telematics are affecting the construction and industrial equipment industry, with compliance being one,” said Conner. “On the compliance side, we can manage the equipment. We can actually recertify operator training all through the telematics system. This is tracked automatically, so if your company requires operators and trainers be trained every year, you can set up calendar reminder dates, things like that, so you know when to retrain the operators.”
Telematics is attractive to company safety departments because of the capability to incorporate compliance requirements and auto-track metrics which can then be recorded and saved digitally, which increases efficiency.
“I think that telematics naturally occurred with the development of technology but there were probably some driving forces behind it, too,” said Conner, referring to the implementation of telematic technology within equipment fleets. “I think safety departments were a big push for this because typically, with telematics, you can incorporate compliance checklists. So we’re getting away from the paper trail, everything can be filed online, in the cloud. So, as far as complying with OSHA, and some of the safety aspects of particular companies, it’s a lot more manageable with the telematics system.”
The future of telematics in the equipment industry
Telematic technology has transformed the way companies track maintenance schedules, assess impact damage, track operator productivity, meet compliance requirements, locate equipment and more. Telematics is expected to further progress and offer fleet owners more advanced features and capabilities.
“Telematics has already progressed quite a bit and I think that we’re really just at the beginning of it,” said Conner. “I think there’s going to come a time when you can purchase a telematics system that’s totally customizable, per specific customer needs. There’s some software out there now that will actually cause forklifts to slow down in certain areas, if you have a really highly trafficked pedestrian area in a plant for example, which minimizes accidents. Once the forklift goes into this location it will automatically slow down until it reaches certain parameters where it will then go back to standard operation.”
The full potential of telematic systems is yet to be seen, but is expected to continue progressing with the development of computer applications, improved processing power and fleet owner needs/expectations.
Back to News
Subscribe and unlock cutting-edge equipment insights, trends and tips!
Subscribe