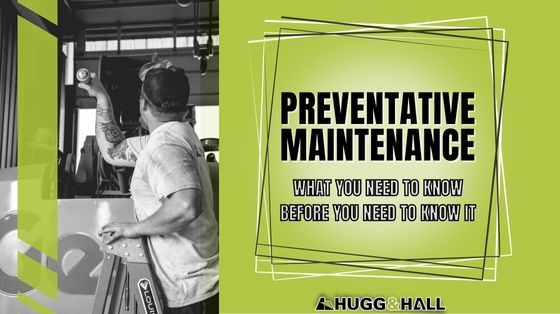
How to Perform Preventative Maintenance
Interested in learning how to perform preventative maintenance? Want to know more about why it’s important? Read on to learn how to create a PM schedule.
Why it’s important to perform PM
It can be annoying to schedule preventative maintenance when you don’t see any immediate issues with your machinery. It’s easy to reason, “Everything looks okay. I can put off a service call.” But the goal of PM is to anticipate wear and tear that will cause more problems down the line. PM can extend your equipment’s lifespan and keep unexpected downtime to a minimum.
Preventative maintenance (PM) can also save you money. Some studies estimate that performing regular maintenance can reduce your total repair costs by up to 25%. Service teams can catch would-be issues quicker when they regularly service your machine, and by performing regular repairs, they can prevent new issues from forming. It can even improve the resale value of your equipment. Check out this article from MaintainX for an in-depth explanation of how PM saves money.
How often should you schedule preventative maintenance?
Unfortunately, there’s no easy answer. PM needs will be dependent on your specific equipment. Always cross-reference your PM schedule with the equipment’s manual. Many service departments will keep you on a PM schedule. Having an existing relationship with a service team can also help you when you need emergency maintenance performed, because you won’t have to hunt for a tech when something’s already broken. Your service records will also be stored with that team already, making it easier for them to know what’s happening.
Understanding preventative maintenance schedules
PM programs typically cover three main components.
- Routine scheduling for oil/filter changes, lubrication, and fluid analysis
- Visual inspections
- Proactively replacing parts before old parts cause problems
Keeping a PM schedule gives you documented proof that you’re maintaining your machinery according to the manufacturer’s recommendations. This record supports any warranty claim you may need to make. Keep a printed or written record of the date of service, what type of service was performed, what parts were replaced, and when the next service will be required.
How often should you schedule preventative maintenance?
Unfortunately, there’s no easy answer. PM needs will be dependent on your specific equipment. Always cross-reference your PM schedule with the equipment’s manual. Many service departments will keep you on a PM schedule. Having an existing relationship with a service team can also help you when you need emergency maintenance performed, because you won’t have to hunt for a tech when something’s already broken. Your service records will also be stored with that team already, making it easier for them to know what’s happening.
Train your team
It may not sound like preventative maintenance, but training your employees is one of the easiest ways to support PM. Certified or knowledgeable operators know how to start and run the machine. They know what tasks they need to complete to make sure the machines work properly, and they know when the machine is acting different. They may even be able to point to specific parts or pieces that aren’t functioning correctly.
On-site PM & PM checklist
Your team can perform preventative maintenance too. If you own your equipment, you probably don’t want to call a service tech every time you finish a job. It’s important to check all items on your PM checklist after completing a major project. You can download this handy PM checklist and store it with your machine.
Pre-start
- Check for overhead hazards (such as power lines) or tripping hazards.
- Look at the coolant package to ensure there’s no dust, dirt, or debris.
- Check engine oil levels, power steering fluid levels, windshield washer fluid levels, and DEF tank (if applicable).
- Check for damage and signs of premature wear and inspect the overall condition.
- Check the belts for cracks, frays, and splits.
- Ensure hoses aren’t loose, pinched, or cracked.
- Look under the equipment for leaks.
- Check tires for pressure, damage, and wear. Ensure valve stems are secure.
- Inspect battery cables, clamps, and connections for corrosion or loose connections.
- Check the cab, windshield, wiper blades, mirrors, horn, and seat belts for damage or visibility issues.
- If you see any signs of missing or loose bolts, fluid leakage, exposed wires, frayed hydraulic hoses, etc., call your maintenance team immediately.
Warm-up
Perform these checks after the equipment has been running for five to ten minutes.
- Check for air filter warnings. Clean or replace the filter if necessary.
- Check the gauges to ensure the machine is operating at safe levels.
- Test all lights.
- Test that the brakes are working properly.
- Check the fluid levels of the engine, steering tank, hydraulic oil, power terrain, coolant, and swing drive.
- Test all hydraulic lines and systems.
- Listen for any unusual noises.
- Monitor all gauges.
- Feel for excessive vibrations.
Shutdown
- Fill the fuel tank.
- Idle the engine for five minutes before shutting down completely.
- Park the equipment in a safe place and engage the parking brake.
- Clean debris off equipment.
If your team comes across something you can’t fix on the yard, always call a service tech. Contact Hugg & Hall’s standard-setting team!
Back to News
Subscribe and unlock cutting-edge equipment insights, trends and tips!
Subscribe