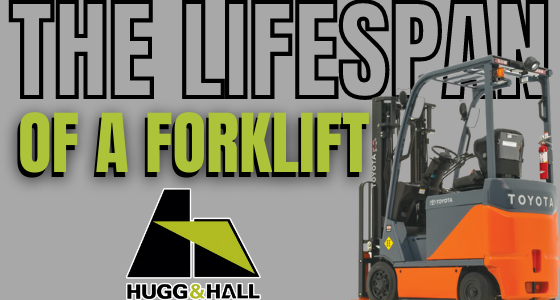
Average Lifespan of a Forklift
Forklifts, like any heavy machinery, are a pricey investment. You want to make sure you’ve...
Forklifts, like any heavy machinery, are a pricey investment. You want to make sure you’ve...
By now, you may have heard of the upcoming changes to ANSI standards for aerial...
Genie has introduced the release of two "high float," ANSI-compliant boom lifts. The lifts are engineered...