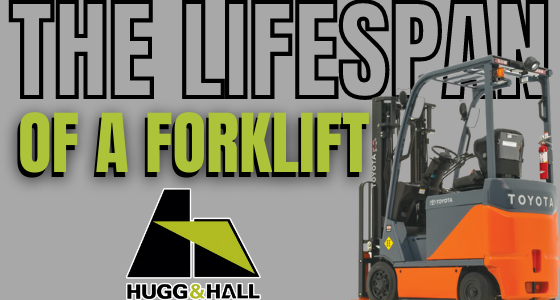
Average Lifespan of a Forklift
Forklifts, like any heavy machinery, are a pricey investment. You want to make sure you’ve...
Forklifts, like any heavy machinery, are a pricey investment. You want to make sure you’ve...
In order to comply with the high standards that Toyota Material Handling expects of their...
Electric Equipment: Transforming Construction As we work together to shrink humanity's carbon footprint, more equipment...
Hugg & Hall Equipment Company (Hugg & Hall) parts professionals, Michael Cooper and Josh Napier,...