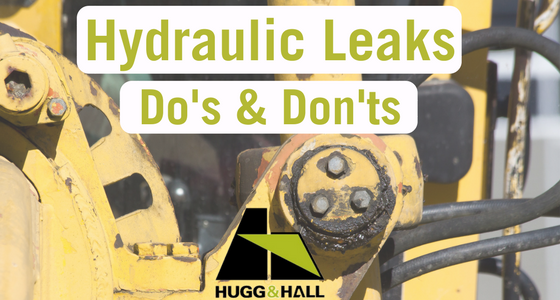
Hydraulic Leak Do’s & Don’ts
Chances are, if you work around or with construction equipment, you have seen or had...
Chances are, if you work around or with construction equipment, you have seen or had...
There is a lot of pressure on your forklift, literally and figuratively. They handle...