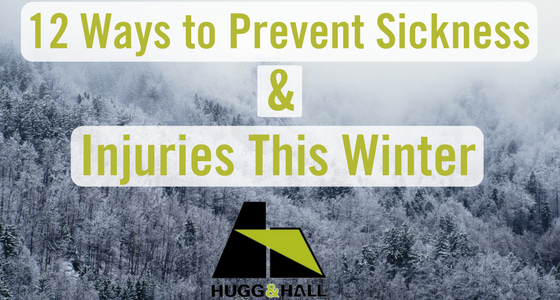
12 Ways to Prevent Sickness & Injuries This Winter
Every season has unique challenges, and winter is no exception. Here are 12 easy tips...
Every season has unique challenges, and winter is no exception. Here are 12 easy tips...
Big changes have been announced for the regulation of certified boom and scissor type platform...
The Occupational Safety and Health Administration (OSHA) has...
Even people who love winter don't love its impact on construction sites. Snow and freezing...