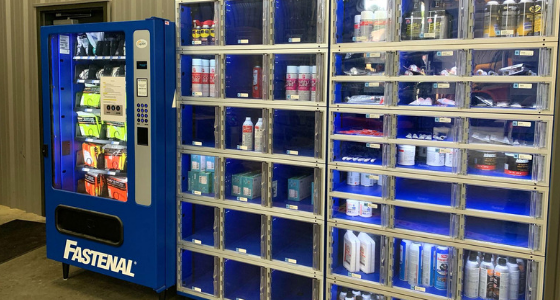
How Service Supply Vending Saves Time & Money
Hugg & Hall Equipment Company (Hugg & Hall) recently installed Fastenal vending machines at the...
Hugg & Hall Equipment Company (Hugg & Hall) recently installed Fastenal vending machines at the...
As about 38 percent of U.S. workers sleep less than seven hours a night, according...
The Hugg & Hall Equipment Company (Hugg & Hall) Product Support Team gathered for a...
Today, after 47 years of dedicated service to Hugg & Hall Equipment Company (Hugg &...
As part of the new ANSI A92 updates, companies will be required to track and...
Before operating portable light towers, it’s important to understand the basic rules of use. The...
Team members from the Hugg & Hall Equipment Company (Hugg & Hall) Jonesboro branch recently...