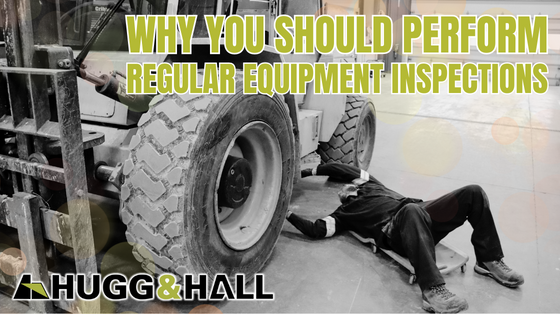
Why You Should Perform Regular Equipment Inspections
It’s a simple idea: if you don’t notice a problem with your equipment, you probably won’t call a technician. It sounds obvious, but equipment inspections are one of the first safety tasks that get skipped when companies are strapped for time.
A routine inspection is one of the easiest way to protect your equipment and your team. It’s a small time investment that pays you back dividends.
It’s vital to perform inspections on your equipment before each use. Identifying potential hazards before they become dangerous can save you time and money and—more importantly—can help protect your staff.
Maintaining a safe work environment for your employees is easier when your equipment is in good condition. Most jobsite injuries are preventable, especially those that occur from employees working with or around damaged equipment. Being proactive and requiring a daily inspection can prevent accidents and injuries.
Damaged equipment should immediately be repaired to prevent injury to your workers. The bare minimum for equipment, according to OSHA, includes:
- A working brake system, including emergency brake and parking brake
- Working headlights, taillights, and brake lights
- A horn or other audible warning device
- A windshield with windshield wipers in good condition
Accidents are more likely if any of these requirements aren’t met and the equipment is damaged. A broken horn or failing brakes can lead to a crash (into a worker or another piece of equipment). Damaged windshield wipers or broken headlights can make it harder to see obstacles.
While you’re implementing equipment inspections, learn how to avoid common jobsite injuries and keep your team even safer.
Inspections can also help you avoid downtime and save you money. Since equipment failure causes projects to grind to a halt, it’s in your company’s best interest to be proactive. You can optimize your equipment’s performance and productivity with regular inspections.
Catching damage or wear early is the easiest way to protect your machinery. Inspections offer compounding benefits: a piece of equipment in good condition, serviced when needed, is significantly more efficient long-term than one that only gets scheduled PM. The earlier you catch an issue, the easier (and usually cheaper) it is to fix.
You’ll get a better return on your investment if you only run highly efficient equipment. Heavy equipment is not cheap, so small repairs are worth the time and cost. Regular inspections can even lead to lower repair costs over time, because small issues are less likely to become catastrophic issues.
Check out this article from MaintainX for an in-depth explanation of how inspections and PM save you money.
You can establish a consistent inspection routine with your team. They are the first line of defense against equipment failure.
Certified and knowledgeable operators are often the most qualified people to perform inspections. Since they run the machines often, they typically know when a piece of equipment is performing differently. They can even point to specific parts or pieces that aren’t functioning correctly.
When you implement daily inspections, you may encounter pushback if you didn’t previously require them. Inspections can seem like a waste of time when a person hasn’t dealt with the effects of broken equipment firsthand. You can require your team to fill out a daily inspection checklist until it becomes a habit.
Train your team members to look at the following things when performing a daily inspection:
- Tire pressure and condition
- Fluid levels
- Fuel and oil leaks
- Brakes and lights
- Mirrors and glass
- Horn
- Seatbelts
- Emergency brake
- Steering
- Attachment condition
This list primarily covers the issues your team is likely to come in contact with. A skilled technician can perform a more in-depth inspection of internal components during PM or a scheduled maintenance check.
Your equipment’s owner’s manual should recommend how often maintenance is needed. Contact a technician if you have questions about specific pieces of equipment.
When your PM is due or you need a more thorough inspection, it’s important to call a trained service tech. Aside from regular PM, you should also get your equipment professionally inspected after the following situations:
- You suspect it’s been damaged
- It has been exposed to conditions that could cause damage (including weather and environmental conditions)
- There are signs it needs repair (like signals, noises, or obvious damage)
- It is going to a jobsite where it’ll be used a lot or be used for a tough job
If your team comes across something you can’t fix on the yard, contact Hugg & Hall’s standard-setting service team!
Regular inspections are vital for safety and efficiency. They keep your team out of harm’s way and keep your equipment running more efficiently. Protect your investment and get the most out of your equipment by updating your equipment management strategy. Perform daily inspections and watch your productivity rise!
Back to News
Subscribe and unlock cutting-edge equipment insights, trends and tips!
Subscribe