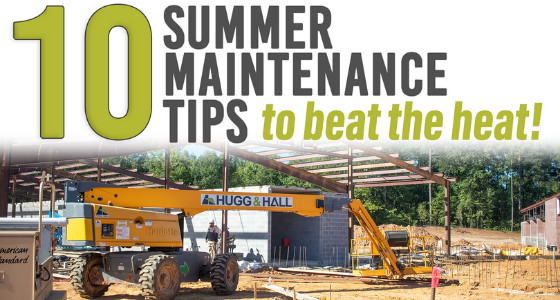
Tips To Keep Your Equipment Up & Running In The Heat
For equipment owners, warmer temperatures require summer equipment maintenance routines. Here are some tips for...
For equipment owners, warmer temperatures require summer equipment maintenance routines. Here are some tips for...
Optimizing Engine Efficiency Through Maintenance Performing regular service on your equipment can help optimize your...