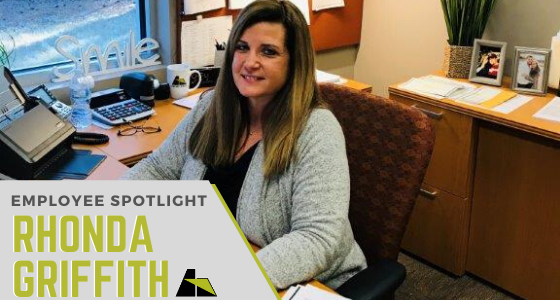
Employee Spotlight: Rhonda Griffith
Meet Rhonda Griffith! Rhonda has been with Hugg & Hall for 20 years and works...
Meet Rhonda Griffith! Rhonda has been with Hugg & Hall for 20 years and works...
product support Over the last 60+ years, Hugg & Hall has strived to be superior...
“There are employees that work hard daily who may not get an “atta-boy”, “great job”...
What are proximity alarms? Proximity alarms are sensors that allow equipment operators to detect people...
Safety should be the most important priority on any job site and equipment should be...
Forklift safety is vital to keeping your warehouse running smoothly. Here are seven forklift safety...