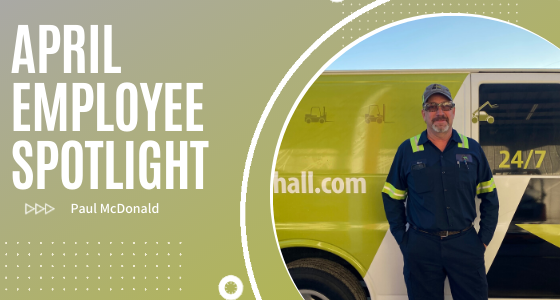
Employee Spotlight: Paul McDonald
Meet Paul McDonald! Position at Hugg & Hall: Field Service Technician, New Orleans branch What’s...
Meet Paul McDonald! Position at Hugg & Hall: Field Service Technician, New Orleans branch What’s...
Anyone who owns or manages heavy equipment eventually faces this question: is it better to...
What's new: Temps are rising and the busy season is almost upon us. What it...