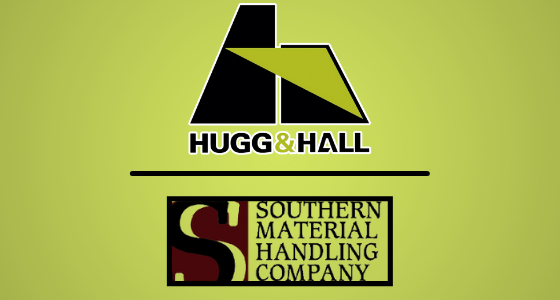
Hugg & Hall Equipment Company Announces Acquisition Of Southern Material Handling Company
Dealership Expands to Provide Full Line of Equipment Needs to Eastern Oklahoma LITTLE ROCK, ARKANSAS...
Dealership Expands to Provide Full Line of Equipment Needs to Eastern Oklahoma LITTLE ROCK, ARKANSAS...
Forklifts, like any heavy machinery, are a pricey investment. You want to make sure you’ve...
There’s no way to perfectly protect from theft, but there are some measures you can...
Forklift safety is vital to keeping your warehouse running smoothly. Here are seven forklift safety...
The use of telematic technology, i.e. telematics, is transforming the way equipment companies manage and...
Hugg & Hall Equipment Company (Hugg & Hall) is committed to transparency and keeping customers...